随着半导体制造业的快速发展,对产品质量的要求不断提高,对微分析技术的需求也越来越高。除了集成电路(IC)制造,纳米结构在新型元件中的应用也日益增多,特别是在纳米光子学和纳米光学领域。 聚焦离子束(Focused Ion Beam,FIB)系统是在常规离子束和聚焦电子束系统的基础上发展起来的。除了具备扫描电子显微镜的成像功能外,由于离子具有较大的质量,经过加速和聚焦后,FIB系统可以对材料和器件进行微纳加工,如刻蚀、沉积和离子注入,因此在纳米科技领域发挥着越来越重要的作用。 FIB加工是通过离子束轰击样品表面来实现的。在FIB加工系统中,来自液态金属离子源的离子束经过加速、质量分析和整形处理后聚焦在样品表面。离子束的斑直径已经可以达到几个纳米,加工方式是将高能离子束聚焦在样品表面逐点轰击,通过计算机控制束扫描器和消隐组件来实现特定图案的加工。 针对具体实验结果分析各加工参数对刻蚀结果的影响,主要讨论了在微纳图形加工过程中,FIB系统工作参数对刻蚀结构的影响。在FIB刻蚀过程中,离子束强度会影响束斑的聚集性;改变离子束的入射电流直接影响离子束的刻蚀速率;随着离子束驻留时间的增加,再沉积效应的影响变得更加明显。熟练掌握各参数对溅射刻蚀的影响,在实际刻蚀应用中能够显著提高加工效率,同时减少因选择不当的加工参数而导致的加工错误可能性。 离子束强度的影响
离子源聚焦到样品表面时,其能量呈高斯分布,设计简单实验初探能量对结构的影响对下一步实验具有指导意义。为方便客户对材料进行深入的失效分析及研究,金鉴实验室具备Dual Beam FIB-SEM业务,包括透射电镜( TEM)样品制备,材料微观截面截取与观察、样品微观刻蚀与沉积以及材料三维成像及分析等。
实验方法:本文研究的各微纳图形均在Si(100)晶片上进行,预先将其切割为需求大小(5mm*10mm)。每次实验前会通过光学显微镜在晶片上查找一块干净区域,并在此区域周边滴上银胶标记,既能方便定位查看结果,又能利用银胶边缘结构快速聚焦。在刻蚀中,纳米图形结构轮廓、形貌特征与不同的工艺参数密切相关。
实验内容:在其他参数一致的情况下,改变离子束强度,研究离子束强度的高斯分布对实验结果的影响。设定结构尺寸为2um*2um,驻留时间为50us,深度设置为100nm,离子束能量取5keV、30keV,研究离子束能量的改变对刻蚀结构的影响。
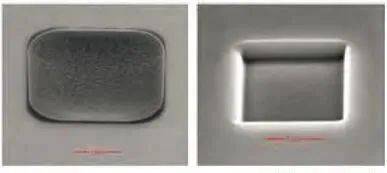
图1 不同能量下刻蚀方形结构的倾斜视图
图1 为两种能量下刻蚀方形结构的52°倾斜视图。根据标尺测量知,5keV 时矩形宽度为3068nm,30keV时矩形结构宽度为2269nm,刻蚀宽度分别比设定的参数大53.4% 和13.45%,由于入射离子剂量相同,实验结果表明,刻蚀中5keV 时束斑更宽,而入射离子速度变慢,刻蚀能力变低,聚焦性更差。因此在实际应用中,根据需求选择不同的能量可以达到不同的效果,如透射电子显微镜(TEM)制备过程中,粗切时就需要选用30keV 进行材料去除,而在减薄过程中则可以选择入射速度较小的离子轰击,慢慢减薄。
另外,从图1(b)中可以观察到,设计的方形结构轮廓,结构的边缘并非垂直侧壁。这是由于入射的束流轮廓呈高斯分布的原因,去除材料主要由能量在半高宽以上的离子分布决定,而半高宽以下分布的离子(beam tail)导致刻蚀出的侧壁非垂直形貌。
离子束电流的影响
离子束电流的增加导致入射离子剂量随着增加,不同电流扫描同样的结构时,电流越大结构轮廓尺寸也会越大。设定三组线结构实验,相同参数包括:不同电流下刻蚀的线轮廓长度均为10us,驻留时间是50us,扫描总时间为20s;三组实验中电流变化依次为1.5pA、9.7pA 和48pA。图2中结果为线结构俯视图,由于线结构轮廓尺寸较小,很难观察到,因此采用原子力显微镜(AFM)对尺寸进行测量,主要对比结构的宽度和深度变化情况。
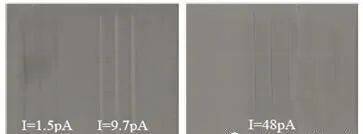
图2 不同电流下刻蚀线结构的俯视图
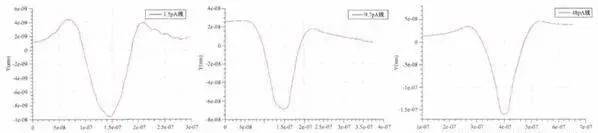
图3 不同电流下刻蚀线结构的AFM轮廓图
图3分别为入射电流1.5pA、9.7pA 和48pA 线结构的原子力显微镜(AFM)轮廓结果,根据AFM测量结果量取三种电流下线结构深度和宽度,如图4所示。
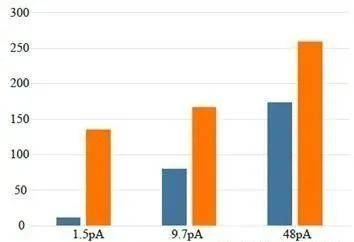
图4 不同电流下刻蚀线结构尺寸
线结构的AFM 测量结果表明,随着电流的增加,入射的离子数增加,相同的时间内,电流越大刻蚀的线轮廓越深,宽度变化比较缓慢。小电流可用来刻蚀纳米级尺寸,大电流材料去除能力较强,实际应用中应当根据不同的需求选用不同的电流进行加工。
离子束驻留时间对结构形貌的影响
FIB加工过程中,在单点停留时间称为驻留时间。在蚀刻过程中,当入射离子驻留时间增加时,再沉积效应随之产生,此时刻蚀的形貌结构由于再沉积影响发生变化,因此在测量溅射产额时,研究驻留时间变化对结构的影响是有必要的。
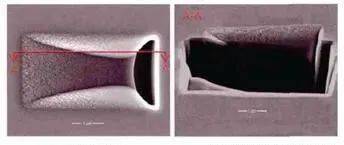
图5 1ms驻留时间刻蚀再沉积结构和截面图(A-A)
如图5刻蚀矩形2um*4um 结构,驻留时间选择1ms,刻蚀1次,扫描方向为从左到右。从截面结果可以看到,整个扫描过程中,一次刻蚀深度曲线式加深,并从开始边界到结束始终有再沉积存在,并在两侧壁形成再沉积非晶层。
再沉积对结构形貌的影响
当驻留时间较长时,再沉积效应会显现出来,利用这一效应可以刻蚀出一些奇特的形貌轮廓。例如,在图6中,首先使用较短的驻留时间(50微秒)对方形结构进行预先刻蚀,扫描次数为20次;然后将驻留时间增加至1000微秒后,对矩形结构进行加工,扫描次数为1次,要求这个矩形结构与方形结构的边缘相交。
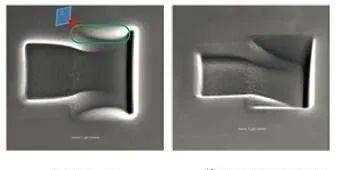
图6 再沉积结构
再沉积效应在第二次刻蚀矩形结构时发挥了重要作用。具体来说,当面对具有一定深度的结构时,由于边界侧壁呈非垂直结构,当扫描矩形结构刻到倾斜边界时,去除材料的能力增加,导致刻蚀速度增大。在这种情况下,会形成两侧类似肋板的结构,这是由于再沉积堆积具有一定的方向性。
在第二次结构初始扫描时,与方形结构重叠的作用会形成一个方形轮廓,后续的再沉积过程会沿着这一方形轮廓继续堆积,最终形成类似肋板的结构。这种现象说明再沉积效应在微纳加工过程中扮演着重要角色,影响着结构形态的形成。
通过对这些实验现象的观察和分析,可以更深入地了解再沉积效应对微纳加工过程的影响。这种了解有助于优化加工参数和控制加工过程,以获得更精确的微纳加工结果。
发表评论 取消回复