贯穿式产品最大的挑战就变形的控制,其他和传统灯具比较起来没什么技术性难题,关于变形的控制,下面重点介绍一种方法,通过DOE实验设计结合Moldflow,在模具设计前期分析出主演根源,提前规避。原始方案产品翘曲变形为-0.71~0.40mm,较大, 超出公差要求:通过Moldflow软件对变形因子进行隔离(与DOE结果一直)
分析结果显示,壁厚和保压压力对变形影响最大,增大壁厚和保压压力,变形会显著减小。将底部壁厚改为DOE推荐值1.5mm(1+30%)=2.0mm按底部壁厚推荐值2.0mm设变产品,变形结果:-0.27~0.37mm,达到产品要求。电镀工艺目前行业没有技术壁垒,有的顶多就是产能问题,例如 贯穿灯饰框,那么长家里没有2000以上的炉子的就痛苦了;关于电镀要解释一个概念,也是很多人搞不清楚的,例如,有些朋友会经常遇到这种情况,客户或者厂商告诉你某个产品是PVD实现的;如果你对PVD不是了解,你可能就会以为什么先进工艺,其实看完下图你就明白的。也就是说,真空镀都可称为PVD,所以当再有人和你说到PVD时,你就清楚了不是吗。真空电镀本身对环境友好,且有出色的色泽表面,对产品形状适应性强,方便批量生产,未来视乎还没有出现更优的工艺方案。但是有些造型的需求,需要在产品表面进行局部电镀,也是就是行业内叫的遮蔽电镀。遮蔽电镀存在一些外观缺陷不足以及生产效率低的问题,例如,溢电或者漏电外观问题。针对此问题,我们倒是开发一种替代工艺,因为还未在行业普及,不变透露。其实这是行业内电镀标识,其含义为:塑料使用电镀光亮铜10μm 以上,光亮镍15μm 以上,普通铬0.3μm 以上。更详细介绍可参阅《不同真空镀膜技术的原理、优势及缺陷》,文中详细介绍了各种真空电镀的原理,优势与劣势对比以及问题处理方法。由于注塑工艺及某些注塑 产品的形状不可避免地会导致注塑件残余应力 的产 生 。而这些残余应力不仅影响产品的几何形状 ,同时 也影响着力学 、光学等性能 ,还可能使产 品在使用过程 中发生开裂等后果 ,是影 响塑料产 品质量不可忽视 的 重要因素。注塑件的残余应力主要分为流动残余应力和热残 余应力。流动残余应力 主要 是在注射 过程 当中形成 的 ,与成型工艺有关 ;热残余应力是 由冷却时注塑件的 温度不均匀 引起 收缩不均匀造成 的 。目前降低注 塑件残余应力的方法主要包括调整注塑阶段的工艺参数和通过退火后处理的方法来实现。退火工艺及参数的具体方法,建议参考《退火对注射成型P制品力学性能的影响》 化学公报,本人不再详细阐述。关于贯穿灯的退火方式,需要强调的是不要试图通过退火来达到矫形的目的,可能适得其反,增加产品的应力。退火需要在一个不受外力的情况下,适当温度和时间使产品残余内应力得以缓解,注意是缓解并不是去除。如果增加外力,可能反而会增加内应力。经常能听到,在退火炉内增加仿形矫形工装的情况,建议还是尽量取消,变形还是那么退火之后得残余应力应如何检测呢?相信很多工程师都为之苦恼,灯具目前没有行业统一测量标准,不过我推荐使用PCBA应力检测的方式,原理适用,仅产品不同而已,后期有时间做份详细资料阐述下。虽然咱不是喷涂方面工程师,借这模块聊聊车灯起雾这个话题吧,毕竟这是每个车灯工艺都绕不开的问题,不管你是喷涂专业,还是总装、工艺、研发等相关工程师,因为车灯起雾涉及模块很多,例如材料吸水率、CAE模拟的雾气分析结果、结构的设计要求、防雾油漆涂层要求,甚至车间的温湿度都有关系。按照网络词条解释,起雾是由于热的空气遇到冷到空气,水汽凝结成水珠形成雾。当然了这是对雾宽泛的解释,车灯里的雾个人觉得略显高级些,因为灯里的雾是智慧型的,它不会乱出起,它会自己找到工程师只有借助CAE分析才能找到的冷区,在那里着床,成长...。之所以灯内的水汽会知道往冷去跑,那是灯内部的温度场驱动的。灯内的光源,模组等是发热源,散发的热量会向远离这些件的低温区域聚集,当到达狭长的较小空间时,流速降低,附着Lens表面;由于水的表面能值是72达因值,而LensPC(聚碳酸酯)材料的表面灯值仅为46达因值,远小于水的表面能,水汽迅速凝结成水珠,从而形成了我们肉眼看到的雾气。其实这个机理是和前组合灯涂胶前需要对housing进行等离子处理是一样的道理。在咱的《等离子涂胶程序轨迹示教规范》里对表面能也有阐述。知道了车灯起雾的机理,解决它就有了方向,不过目前行业内多数还是没有办法彻底解决,仅是降低发生概率而已。不过奥迪部分车型方案将车灯冷区通过内置管道+外置软管和车身上除湿装置连接,形成主动空气对流,还是挺前卫的,效果应该是不错的,咱没有找到具体方案原理图纸,不过有份专利大家倒可以参考《汽车大灯除雾气装置》 CN201320807564.7 天津海宇光电科技有限公司。不过市场上奥迪起雾却屡见不鲜哦。(2) 根据车灯散热源在灯内分布,适当调整其位置,提升冷区温度,降低温差范围;发光源可以通过调整反射碗光学面增加狭窄或冷区的光源照射,帮助提温,前提是不能影响光学性能。(3)增加饰框Bezel、LensLens、LensHousing之间的距离,增加空气流通的空间,平衡灯内温度场。尤其是饰框和周边件的间隙。(4)喷涂防雾涂层、放置内置干燥机、适当布置通气组件降低水汽凝结。(5)选用吸水率较低的材料,尤其是尽量避免使用PA材料。(6)灯具零部件及总成存储、制造过程控制车间温湿度,在ESD允许的情况下,车间湿度尽量保持最小,建议不超过35%,以避免零部件及总成材料吸水饱和。我们知道,能量输入的结果使得物质发生从固态到液态,再从液态到气态的聚集态变化。如果再将额外的能量输入到气体中,气体将发生电离,并转变为另一种聚集状态,即等离子态。当等离子体和其他物质接触时,所输入的能量被传递到被接触的材料表面,并随之产生一系列的作用。 低温等离子体中的粒子的能量一般约为几个到十几个电子伏特,大于聚合物材料的结合键能(几个到十几个电子伏特),完全可以破裂有机大分子的化学键而形成新键;但远低于高能放射性射线,只涉及材料表面,不影响集体的性能。处于非热力学平衡状态下的低温等离子体中,电子具有较高的能量,可以断裂材料表面分子的化学键,提高粒子的化学反应活性(大于热等离子态),而中性粒子的温度接近室温,这些优点为热敏性高分子聚合物表面改性提供了适宜的条件。通过低温等离子体表面处理,材料表面发生多种的物理、化学变化、或产生刻蚀而粗糙,或形成致密的交联层,或引入含氧极性基团,使亲水性、粘结性、可染色性、生物相容性及电性能分别得到改善。在适宜的工艺条件下处理材料表面。在适宜的工艺条件下处理材料表面,使材料的表面形态发生了显著变化,引入了多种含氧基团,使表面由非极性、难粘性转为有一定极性、易粘性和亲水性,有利于粘接、涂覆和印刷。如果用火焰来处理,其弱点是所有聚合物都是易燃和熔点低的材料。当有机材料置于高温火焰下时,会因受高温的处理而变形、变色、表面粗糙、燃烧、和散发出有毒气体,且处理工艺难易掌握。将使用38dyn/cm的达因笔垂直于测试物体表面,在表面上均匀划一条直线,来判断是否适合涂胶的要求,如果连续成线,没有收缩成小墨滴现象,则表示等离子处理合格。相反,如果断断续续,不成线,并形成墨滴,说明等离子处理达不到涂胶要求。轨迹应保证喷出的低温等离子焰中间橘黄色区域接触物体表面,即物理离喷嘴8~15mm;速度控制在40~60mm/s;轨迹应保证等离子火焰可以覆盖整个胶槽底部表面和侧壁距离底部2/3的表面,喷嘴应尽可能垂直物件表面,如下图:涂胶胶嘴应尽量垂直于被涂胶物件的表面,速度与胶机马达转速相关,一般胶机马达转速在15~25r/min之间,机械手速度在80~120mm/s之间。为防止起点后终点胶枪移动离开胶槽,造成有残留胶丝进入灯内,起点和终点的选择应在机械手回原点的一侧,即机械手无论从原点到起点还是从终点到原点轨迹都不会经过灯具上方;并且涂胶结束时,应在胶槽上方来回运行两次,使胶丝断开,(5)前灯涂胶随着灯具造型和尺寸的复杂化,需要有技术性的突破;复杂多变的造型、贯穿式前灯都将增加的涂胶均匀性的难度。个人预测,7轴甚至更多轴数涂胶单元在不久的将来应该会诞生,类似于传统的CNC加工中心向多轴联动加工中心的改革升级过程。(6)用胶成本也是现在车灯企业面临的现状,贯穿式前灯的诞生将会加剧这个问题的情况;知名车灯用胶配套商汉高、道康宁、以及国产龙头硅胶企业成都硅宝都在布局自己的低成本产品。当然,大家也都知道这种涉及性能,尤其是售后耐候性能,没有哪家车灯企业甚至车厂,敢进行大刀阔斧的切换量产,大家都在小批应用中,甚至还有些在实验阶段。更多用胶知识,大家有兴趣的化可以参与资料《车灯用胶现状2020》 汉高;不再详解。前灯用胶我多提一嘴,随着电气化、数字化的发展,灯具价值不断攀升,假如涂胶完成后,你发现灯内有个小异物,你咋办?报废?返工取出?(LED的应用,灯具后盖将逐渐退出历史舞台)拆灯重复利用内部电子件?可能都不太现实了,不过日系车灯已经给出的答案,大家可以留意下。我后面也还会讲一下激光焊接在前灯密封性上的前景,以及理论和实验分析论证的结果。经常会有人问我,前灯为什么不是用热板或者振动焊接,甚至有问尾灯为什么不涂胶,这也是我刚入行时的疑惑,不过这里面是有很大的学问的,不是简单的成本或耐蠕变性等的问题。最后和前灯激光焊接一起讲讲这个吧。焊接工艺主要应用在尾灯、牌照灯、转向灯等等;当前也有部份企业开始在前后LOGO灯、昼行灯上普及;个人觉得,随着焊接工艺的进步发展,前灯使用焊接工艺那也是早晚的事,毕竟这是一种清洁工艺,且耗材成本。车灯的焊接种类有很多,下面列举一些并说明应用场景: | |
| |
| 尾灯、牌照灯、转向灯、雾灯、昼行灯、Logo灯、回复反射器等等 |
| |
| 牌照灯、转向灯、雾灯等一些小尺寸灯具,也广泛应用在车灯内部零部件焊接,如饰框与饰条焊接等 |
| 我们已经实现量产,效果堪比激光焊接,目前处于保密阶段不便透露 |
以上焊接为目前行业成熟且常用的焊接工艺,新型混合焊接除外;以上每种焊接还可细分,例如,高温热板焊接和低温热板焊接、振动焊接和红外振动焊接、同步激光焊接和轨迹激光焊接等等。多种焊接工艺的存在且成熟又给很多人造成了困扰,到底该选择哪种工艺呢?回答这个问题非常复杂,涉及成本、灯具结构、材料物性、质量要求、人才储备等等。个人觉得没有标准答案,仅有参考条件。S1:确认客户SOR或者质量要求里对焊接的相关要求S2:根据产品结构、材料选用确认能满足客户质量要求的焊接工艺S5:根据焊接人员技能储备和公司未来项目规划锁定最终方案。S1:客户要求A面焊渣0.8mm不允许有,0.5mm允许3个,0.3mm允许5个;装车状态不可见焊接溢料。此步骤排除热板焊接方式,因为热板焊接的溢料很明显,装车状态是可见的。S2:Lens PMMA 赢创8N;Housing ABS30%+PC70% 灯具结构所有焊接方式可满足。此步骤排除新型焊接和传统振动焊接,PC含量较高,100%有较大较多焊渣。S4:治具做1出1,L/R各1幅,共2幅,总预算50万。此预算排除激光焊接。根据以上4步,基本就可以锁定最终方案,就是红外预热振动焊接;不过50万做2幅红外振动焊接治具,需要选择性比较较高的厂商。说完工艺的选择,接下来具体说说每种工艺的具体原理。车灯塑料焊接,本质是通过加热方式使两种材料结合,焊接工艺的命名都是根据提供热量的工艺命名的,例如激光焊接,提供热量的工艺是激光;振动焊接,提供热量的工艺是高频振动。车灯激光焊接工艺近几年才流行起来,较常见的激光焊接方式有轨迹式激光焊接、同步式激光焊接、准同步式激光焊接。轨迹式激光焊接又名顺序型轴线焊接,是指焊接件和激光束按照预定的路线进行相对移动而完成的焊接。随着激光束的移动,焊接材料熔化后冷却凝固从而完成焊接,激光束的移动可以通过机器人来完成。这种激光焊接方式降低了加工成本,减少了工艺破坏。此塑料焊接技术单位成本极低,对于低产量的生产也是如此,因此格外经济。同步式激光焊接是指焊缝同时被多束激光照射加热。同步焊接没有焊缝长度的限制,焊缝也可以不在一个平面,只要夹具的压力沿整个焊缝能够均匀分布即可。同步焊接可以很好地完成同一平面上的焊接,如果是复杂曲面的曲线焊接,需要添加光束整形部件,通过控制和调整光束整形部件使激光能量在整个焊缝长度范围内均匀分布。同步式激光焊接方式生产效率高,适合批量生产。准同步式激光焊接是指轨迹式激光焊接和同步式激光焊接两种方式的结合。准同步式激光焊接中激光束移动的速度比轨迹式激光焊接更快,而且这种方式可以同时加热整个焊缝,从而使焊缝受热更加均匀。另外这种焊接方式产生的溢料较少,加工时间比轨迹式激光焊接短很多。但由于电镜扫描范围的限制,对灯具尺寸有一定的要求,不能过大,同时Lens角度不能过大,不过仍然可以通过采用多个电镜的方法来实现较大零件的焊接。准同步式激光焊接方法适合用于焊接时间短、小尺寸灯具的焊接或需要监控焊接轨迹的焊接。激光透射焊接技术的基本工作原理如图 1 所示。在焊接过程中,两种不同的塑料制品在压力下被夹紧在一起,通过反射镜、透镜或光纤组成的光路系统,将激光器产生的光束聚焦在待焊接区域,激光穿过上方的透射材料,然后被下方的吸收材料吸收,并将光能转化为热能,使得下方的吸收材料升温,并将热量传递到上方的透射材料,在两种材料的接触面形成一个焊接区,在随后的凝固过程中,已融化的材料形成接头,待焊接的两种材料即被连接起来。车灯的Lens和Housing是两种不同的材料。为了实现激光焊接,Lens材料必须能够对激光有极高的透过率,而Housing材料则必须对激光有极高的吸收率。同时,在焊接前必须确保Lens和Housing之间没有凹坑和凸点,当Lens和Housing之间存在凹坑和凸点时,两者之间会存在间隙,且这种间隙无法通过加压的方式去除。当激光照射在Housing焊筋表面时,Housing焊筋产生的热量由于间隙的存在无法传递到Lens上,从而导致间隙处的Housing焊筋温度过高,发生碳化,影响整灯外观,严重时还会影响到整灯的气密性。波长为 980 nm 的半导体激光器输出功率较小,适用于焊接激光功率要求较低的场合,容易被塑料吸收,激光能量转化效率高,易于实现激光器的小型化,方便通过光纤来构建光路。汽车尾灯Lens常用的材料是 PMMA,Housing常用的材料是PC+ABS,测试这两种材料对波长为 980 nm 激光的透过率和吸收率,确定Lens与Housing的材料牌号分别为 PMMA 8N-Clear 和 PC+ABS MAC-601 BK102。图 20 所示的是 PMMA 8N-Clear 材料对不同波段激光的透过率 ( 3 mm) ,图 21 所示的是 PC+ABS MAC-601 BK102 材料对不同波段激光的吸收率 ( 3 mm) 。图21 PC+ABS MAC-601 BK102 对不同波段激光的吸收率两个塑料部件在一定的压力、振幅和频率下,相互接触摩擦。因摩擦产生热量,使得材料在焊缝界面处熔化。在压力下,熔融塑料从焊缝区域流出形成溢料,见图1。在振动停止后,熔融塑料层固化,并产生一个坚固的接头。振动摩擦焊接非常适合于焊缝处在一个大平面、相容性热塑性材料的焊接,能够实现高强度、承压大和高密封的焊接性能,是一种非常精确和高重复性的连续生产过程。其过程类似于将两个手掌互相压紧、来回移动产生热量。振动摩擦焊接过程可分为四个不同的阶段,分别是固体摩擦阶段、固液相变阶段、稳态流动阶段和冷却阶段,见图22。几乎所有的热塑性材料都可以采用振动摩擦焊接,包括结晶,无定形、填充、发泡和增强型塑料。无定形塑料如PC,比半结晶更容易焊接。该工艺不适合于非常柔软的材料如TPC。热固性塑料不能焊接,因为其分子链已经发生化学交联,无法扩散。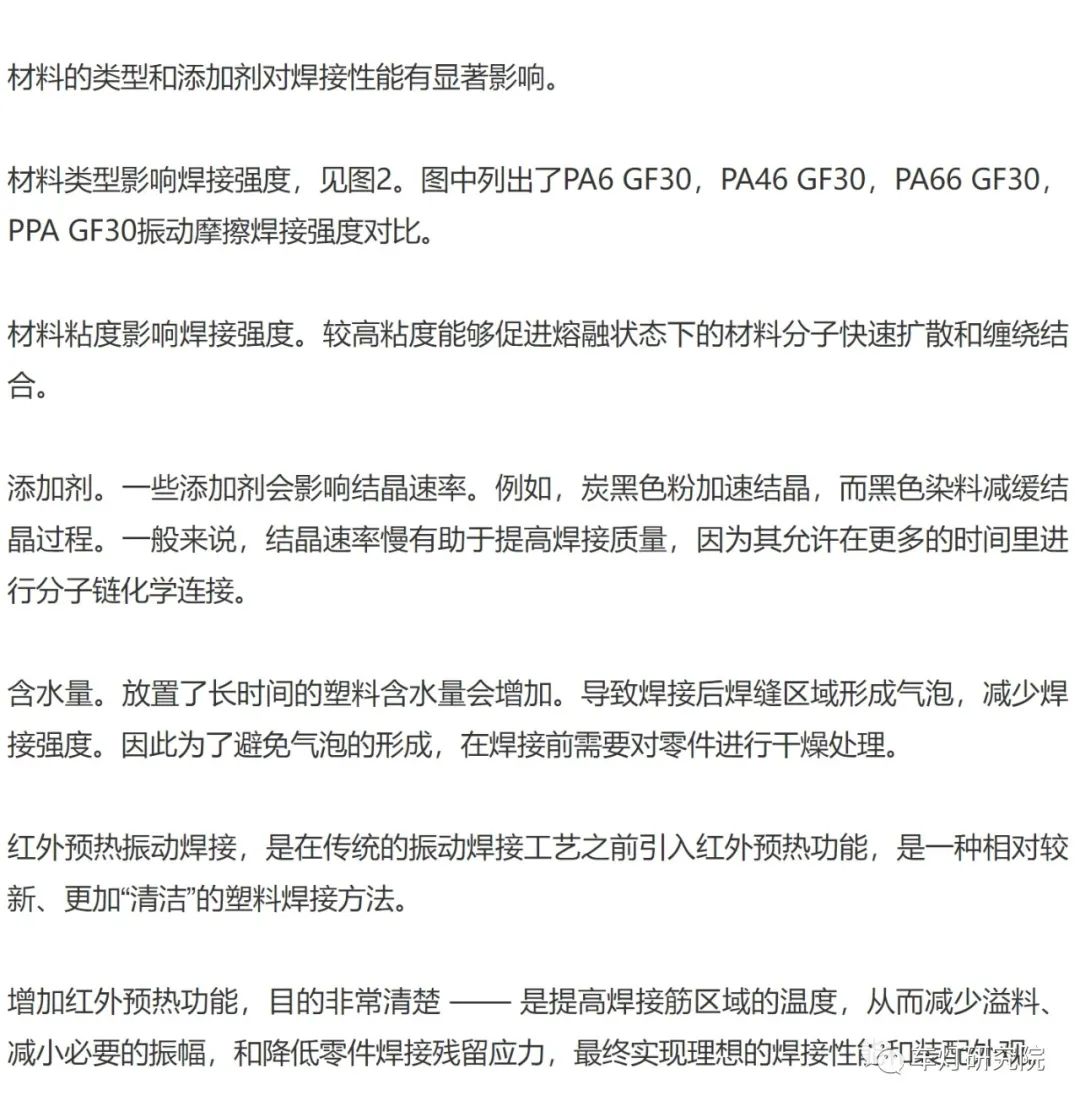
从上图可以看出红外预加热振动焊接可以使不同材料快速的在同一时间达到焊接温度,避免焊接缺陷。红外焊接相比与传统振动焊接以及激光焊接,是当下主流的焊接方式,一是工艺应用较为成熟,在传统振动焊接上进行优化无论工装治具、设备、工艺参数甚至产品设计都沿用传统的方式,不激进风险小。二是相比与激光焊接,无论工装治具还是设备甚至技术人才的成本都是比较低的,三是焊接强度、外观质量介于传统振动或激光焊接之间,基本满足大部分车厂或终端用户的需求;激光虽好,可是有几个终端用户会关注并且为此买单呢。步骤1:上料:两部分工件通过真空气压差,被垂直吸附在热板焊接机上步骤2:加热:铝制预热板被放置在两工件之间,温度一般在50°C-100°C,两工件的焊接处被加热熔化步骤3:焊接:移除铝制加热板,上下工件垂直方向移动,直至两工件焊接面接触,完成焊接
发表评论 取消回复